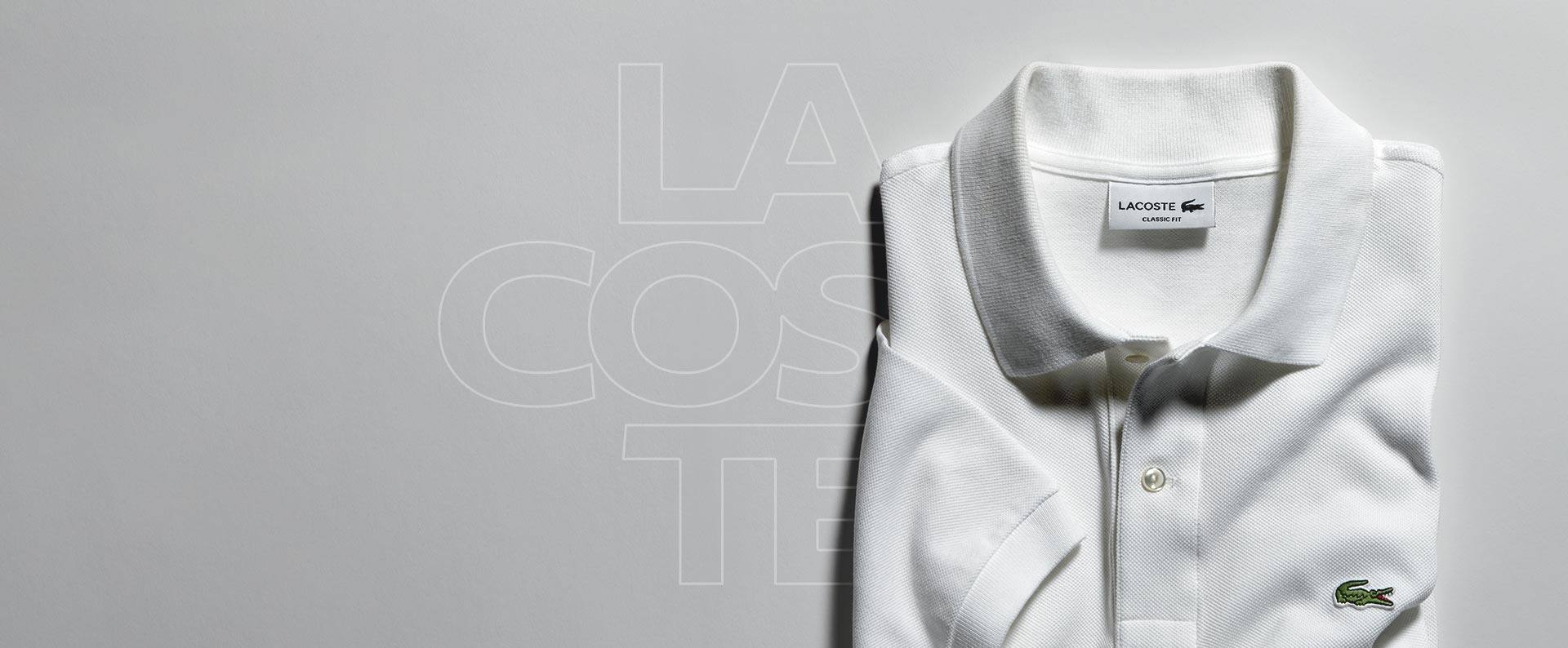
The Polo: 4 Steps for 1 Shirt
Before it can add elegance to your style, the Lacoste polo goes through these four stages.
The knitting
A knitting machine is composed of no less than 2500 needles.
The dyeing
The dyeing process lasts 9 hours on average.
The crocodile’s seal
It requires 1200 stitches.
The assembly
The polo undergoes 25 quality control checks. When finished it weighs 230g.
Material Evidence
Petit Pique or diamond weave taffeta? Discover the iconic Lacoste materials.
Petit Piqué
Created by René Lacoste, the emblematic Petit Piqué is made of fibres knit together at two different levels of tension. The result? A finely honeycombed fabric that enables air to circulate freely. Breathable and lightweight, this fabric ensures comfort, ease of movement and elegance.
Diamond Weave Taffeta
Made in the 90s, this hard-wearing fabric lends Lacoste’s tracksuits and caps a solid criss-crossed weave. Designed for freedom of movement, it is supple and lightweight, dries very quickly and doesn’t crease. Lined with jersey or cotton, this is clothing for sport or comfort. Its diamond motif gives a bright, quilted texture, the signature of Lacoste’s priceless know-how.
Troyes, France in three key numbers
160 kilometres is the distance between the French knitwear capital and Paris. It’s not surprising then, that this is where René Lacoste established a manufacturing base to make the first polos. 1933 was the date production of the first Lacoste polos began in the Troyes factory, under the name La Chemise Lacoste. 40 minutes is the average length of time required by a garment-maker to assemble your polo like a puzzle.
Tracking the Crocodile
Everything you always wanted to know about Lacoste but were afraid to ask.